Material Handling Equipment Types: The Ultimate Guide
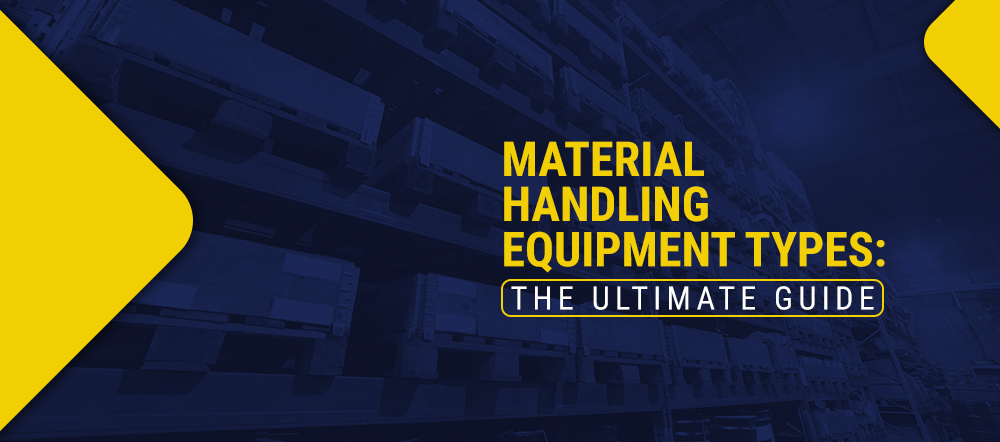
If you handle materials in a warehouse or other facility, you likely have to handle many products and materials. One of your most important duties is ensuring these materials aren’t damaged during storage and that they quickly move through your various production processes. Without the proper equipment and systems in your corner, your company is more likely to damage products and fall behind on your productivity targets.
That’s when material handling equipment can help. Learn more about the main categories of warehouse material handling equipment and why it’s so important to have in your warehouse below.
Table of Contents
- What Is Material Handling?
- Types of Material Handling Equipment for Warehouses
- What Is the Importance of Material Handling Equipment?
What Is Material Handling?
Material handling encompasses a comprehensive set of activities focused on storing, controlling, protecting and moving products and materials throughout their lifecycle. Effective material handling ensures seamless operation and minimizes disruptions within the supply chain from the moment raw materials enter the production process to the point of final product distribution.
Types of Material Handling Equipment for Warehouses
An extensive range of equipment and systems are available to cater to diverse operational needs. These solutions span from manual, labor-intensive methods to cutting-edge, fully automated systems, each offering unique advantages and applications. Explore the four primary types of MHE below.
1. Storage and Handling Equipment
Storage and handling equipment holds materials when they’re not actively in use. Additionally, this equipment is a reliable repository for products at the beginning or end of the production process. Note this equipment is not usually automated. Automated storage and handling equipment are referred to as engineered systems or automated systems.
One of the advantages of utilizing storage and handling equipment is how it improves overall operational efficiency. In a warehouse setting, the effectiveness of the production system relies on the accessibility and swift transportation of materials by equipment and staff.
By enabling the seamless pickup and transport of substantial material quantities, storage and handling equipment facilitates smooth operations and minimizes delays. Creating an efficient system ensures other equipment can efficiently retrieve and relocate materials as needed, optimizing productivity and reducing the risk of operational bottlenecks.
Storage and handling equipment consists of a range of solutions developed to manage materials within a warehouse or production facility. These include:
- Racks:Â Racks are versatile structures that provide vertical storage space, allowing for organized and accessible placement of various items. With options such as pallet racks, cantilever racks or push-back racks, they enable efficient storage of goods of different sizes, shapes and weights.
- Shelves: Shelves offer horizontal storage surfaces with multiple levels, making them ideal for storing smaller items or products that require easy visibility and accessibility. They come in various forms, such as static shelving, mobile shelving or bin shelving, providing flexible storage solutions tailored to specific needs.
- Stacking frames:Â Stacking frames are modular structures designed to stack and protect materials or products, maximizing vertical storage space. They’re handy for items with irregular shapes or items needing extra protection during storage and transportation.
- Mezzanines: Mezzanines are elevated platforms that create additional floor space within a facility. Mezzanines provide opportunities for storage, assembly or office areas, optimizing the utilization of available square footage without extensive construction or expansion.
2. Automated or Engineered Systems
Automated systems are fully mechanized solutions that store and transport materials. Unlike individual equipment units, a computerized system typically comprises multiple interconnected components working together seamlessly.
By harnessing the power of automation, these systems reduce the need for manual intervention, minimizing the potential for errors and improving overall operational efficiency. They can handle complex tasks and large volumes of materials with precision and speed, contributing to increased productivity and optimized workflow management.
One of the most common forms of these systems is an Automated Storage and Retrieval Systems (AR/RS). This type of system will typically be quite large. It features shelves, aisles and racks. A shuttle, a device much like a cherry picker, is used to pickup material and place it on the system. An operator will sometimes manually use the shuttle to pickup items and place them on it, but the picking process can also be entirely automated and computerized.
One major advantage of an AR/RS is that it can be connected to a facility’s computer network. This connection makes it easy for a company to keep an eye on their stock control. The AR/RS can also be integrated with other stages of a facility’s process to make everything more automated.
These automated systems revolutionize material handling operations by providing reliable, efficient and autonomous solutions. Automated systems are categorized into various types, each specifically designed to optimize different aspects of material handling. The primary types of automated systems include:
- Conveyor systems:Â Conveyor systems consist of motorized belts or rollers that transport items along designated paths, enabling efficient and continuous material flow. Conveyor systems are versatile and can be customized to accommodate different materials, including packages, pallets or bulk goods.
- Automated guided vehicles (AGVs): AGVs are autonomous vehicles programmed to handle material transportation tasks within a facility. These vehicles navigate predetermined paths using sensors, magnets or lasers to ensure precise and safe movement. AGVs can transport materials between production lines, warehouses or other designated areas, eliminating the need for manual labor and increasing operational efficiency.
- Robotic delivery systems: These robots can autonomously navigate the facility, picking up and transporting items from one location to another. Equipped with advanced sensors and navigation technologies, robotic delivery systems offer flexibility, scalability and high precision, enabling seamless integration into various workflows.
3. Industrial Trucks and Forklifts
Industrial trucks and forklifts cover a broad category of equipment. The one thing they have in common is that all of the pieces of equipment help with transportation. Industrial trucks and forklifts are available in a range of sizes. For example, you can find something small enough to be hand-operated, and you can also find equipment large enough to be driven.
These industrial trucks come in two main types: stacking and non-stacking trucks. A non-stacking truck is only for transportation. A stacking truck can load products and stack them.
Usually, industrial trucks have attachments like insertable flat surfaces or forks to make the transportation process easier. These attachments to fit under pallets for quick and easy picking.
Industrial trucks lift materials through manual or powered means. Powered industrial trucks usually have a cab, making it easy for the operator to pick up heavy material. Some power-assisted industrial cabs have to be pushed into position but can still lift materials via controls. Additionally, some more advanced industrial trucks can be automated, using optical sensors and predefined pathways to move along the warehouse floor.
Some of the primary types of industrial trucks include:
- Hand trucks:Â Sometimes referred to as a dolly, hand platform trucks are some of the most basic forms of industrial trucks. They usually feature a handle for leverage and a small platform to set heavy objects on that would be difficult to carry. The operator tips the equipment onto the handle and rolls the equipment to wherever the item needs to go.
- Platform and pallet trucks: Platform trucks are a type of hand truck that have wider platforms and sit low to the ground. Pallet trucks, or forklifts, are designed to lift pallets. They’ll slip under a pallet, and then an operator will steer the pallet wherever it needs to go. These types of trucks come in both manual and electrical forms.
- Sideloaders: Sideloaders are built to fit in narrow aisles. They pick up items from different directions, making them ideal when a warehouse is using more of their space by placing aisles close together.
- Walking stackers: A walking stacker lifts and moves materials like a forklift. Though they don’t come with a cab for an operator, they can come in electric versions to assist with transportation.
- Pallet jacks:Â One of the common types of warehouse equipment, pallet jacks are a very basic form of a forklift. They’re used to move materials around a warehouse and are often manually pushed, though there are powered options as well.
- Order pickers: An order picker lifts operators high off of the ground and allow them to get to hard-to-reach materials on high shelves.
4. Bulk Material Handling
Bulk material handling equipment refers to the equipment that stores, controls and transports materials in bulk. Usually, the materials will be in a loose form. This type of equipment typically handles beverages, metal items, minerals, food and liquid.
An example of a bulk material handling system is the use of a conveyor belt to move materials from one area of the production floor to another. You’ll see hoppers and drums funnel loose items into areas where the items can be packaged or manipulated in some way.
Common examples of this type of material equipment include:
- Stackers: These pieces of bulk material handling move items from one point to another. Stackers are automated and will place various items and products onto stockpiles.
- Conveyor belts: One of the key parts of a conveyor system is a conveyor belt. They usually utilize pulleys or drums to rotate the belt and move material on it across a facility.
- Reclaimers: A reclaimer is a large machine used to pick out materials from your stockpile.
- Bucket and grain elevators: Bucket elevators are sometimes called grain legs. They help to transport bulk materials vertically. Grain elevators move materials along a production pathway, as well as store it.
- Hoppers: Hoppers are shaped like funnels and are used to dump or pour materials into containers. They can close off their opening and hold onto the material until it needs to be released.
- Silos: Common on farms, but useful in a variety of facilities, a silo is a tower that holds materials. Common materials stored in silos include grain, woodchips, coal, sawdust and food.
What Is the Importance of Material Handling Equipment?
MHE is crucial for the success of a company as it looks to handle material efficiently. Improper storage and handling can cause product loss, damaged material and inefficiency in your supply chain. To avoid these issues, you should invest in material handling equipment designed for the needs of your company and the materials you handle.
Below are some of the top ways a good material handling system can provide distinct advantages to a company:
1. Reduce Material and Product Waste
A common issue warehouses and facilities face is the need for proper storage systems and the presence of equipment that mishandles materials. Storage issues can lead to products needing to be fixed during storage or transportation. This material waste can lead to higher costs for the company handling the material and dissatisfied clients who expect their products to be well cared for.
Proper warehouse storage equipment will ensure items in your warehouse are stored safely. For instance, stacking frames can help a company keep crushable materials stacked on top of each other without harming the items. Improved warehouse transportation equipment also helps to move materials more efficiently and safely, reducing the chances that materials get dropped or harmed.
Additionally, a material handling system can help companies keep a more accurate track of their inventory. For instance, proper shelving and organizational features help companies know exactly where to find products and keep track of them when they need to be moved. Computerized systems can automatically track your inventory and ensure you always have the correct amount of products.
2. Lower Material Handling Costs
One of the biggest concerns of those using material handling equipment in their business is lowering costs. Much of a company’s production process involves material movement, procurement and storage. These aspects of the process can cost significant money, especially if your material handling system is inefficient. If your material handling system can’t handle the flow of materials efficiently, stoppages can occur, leading to new costs and lower profitability.
Effective material handling equipment and systems are essential for a seamless production process. Fully automated systems eliminate the guesswork in product handling, significantly reducing the risk of user errors. Companies can enhance their material handling capabilities even with proper manual equipment, ensuring efficient transportation from point A to point B.
Companies can optimize operations and minimize disruptions by investing in appropriate material-handling equipment. Fully automated systems leverage advanced technologies, providing precise and reliable handling of products.
The higher initial costs of more sophisticated equipment are well worth it, as they help a company handle more material faster and more efficiently. In the long-term, you’ll lower costs associated with errors, damaged equipment and work stoppages.
3. Greater Warehouse Capacity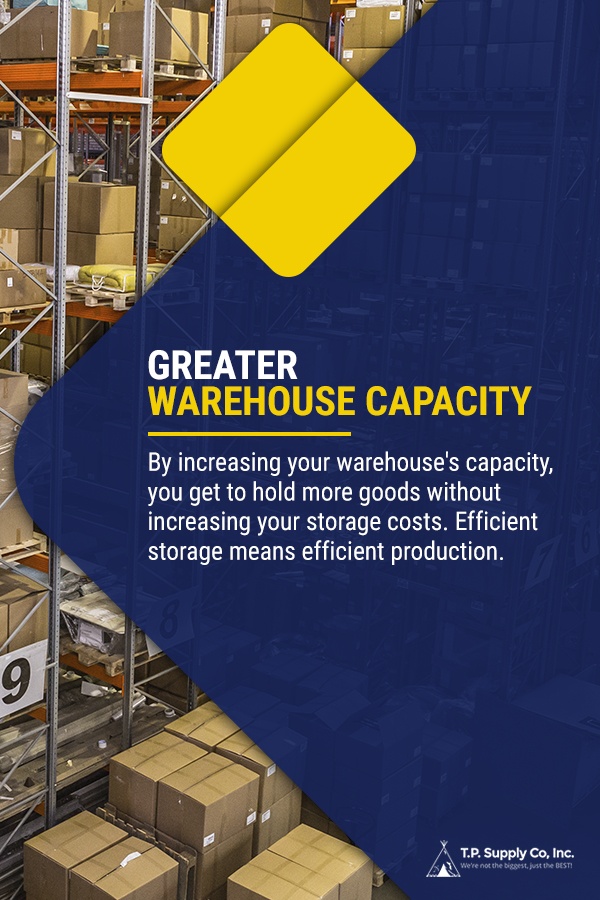
Maximizing your warehouse’s capacity to accommodate a higher volume of goods is a step toward enhancing profitability. By implementing suitable storage and handling equipment, you can effectively utilize a larger portion of your warehouse space, increasing your overall storage capacity.
Investing in appropriate storage solutions allows you to optimize the layout and organization of your warehouse. Properly designed storage equipment enables systematic storage and easy accessibility to goods, reducing the chances of overcrowding or inefficient space utilization.
Sideloaders allow you to place your aisles closer together, as they can easily fit in between them and pick out equipment from either side. Another example of warehouse equipment opening up your floor space is the use of racks, stacking frames and mezzanines. With this storage and handling equipment, you can stack pallets and materials higher safely.
Increasing your warehouse’s capacity allows you to hold more goods without increasing your storage costs. Efficient storage means efficient production. As a result, you can raise your overall production ability and potentially raise your profitability.
4. Better Work Conditions and Worker Safety
Manually lifting materials and transporting them can be very time-consuming and strenuous for workers. Workers can get burnt out doing this kind of manual labor and run a higher risk of injuries. With equipment, you make their work much easier, freeing them up for more tasks and creating a more enjoyable workplace. You also reduce the chance that mistakes happen, which makes it so managers have much fewer headaches to manage during the workweek.
Implementing MHE in warehouses enables workers to perform strenuous tasks with reduced risk of injury. Powerful equipment, such as forklifts, cranes or conveyor systems, empowers employees to handle heavy loads more efficiently and effectively. These specialized tools provide the necessary strength and precision, reducing the chances of accidents or musculoskeletal injuries caused by manual lifting.
5. Enhanced Material Flow
Well-designed storage systems, efficient conveyor systems and reliable material handling equipment ensure the uninterrupted movement of materials throughout the facility. With an improved system and pieces of equipment, you improve your material’s circulation around the facility.
The material will reach the needed stations and locations faster, ensuring your flow stays consistent. A positive side effect of the improved material flow is that it causes materials to stay in your facility for shorter periods of time and gets to consumers faster.
6. Improved Distribution
Your ability to deliver final goods to wholesalers and retailers is crucial to these clients’ satisfaction. Not having MHE and other warehouse equipment can cause you to get your products to clients much slower. Poor storage and packaging equipment and systems can lead to damaged products. Damaged products and slower distribution is a recipe for dissatisfied clients.
With the best material handling equipment in your corner, you can make sure your products are stored safely and distributed properly. A conveyor system, for example, can move products through different stages of the production process and get them in position for distribution.
Contact T.P. Supply Co for Material Handling Solutions
Upgrade your warehouse or facility with top-quality material handling solutions from T.P. Supply Co. As a trusted retailer specializing in warehouse material handling, we offer a wide range of shelving solutions, material handling products and racking systems. When you choose to purchase from us, we go the extra mile by providing expert installation services, ensuring a smooth and efficient setup for your facility.
Browse our selection of material handling equipment to see how we can take your facility to the next level. If you have any questions about warehouse material management, please feel free to contact us.