No products in the cart.
11 Ways You Can Optimize Your Warehouse for 2022
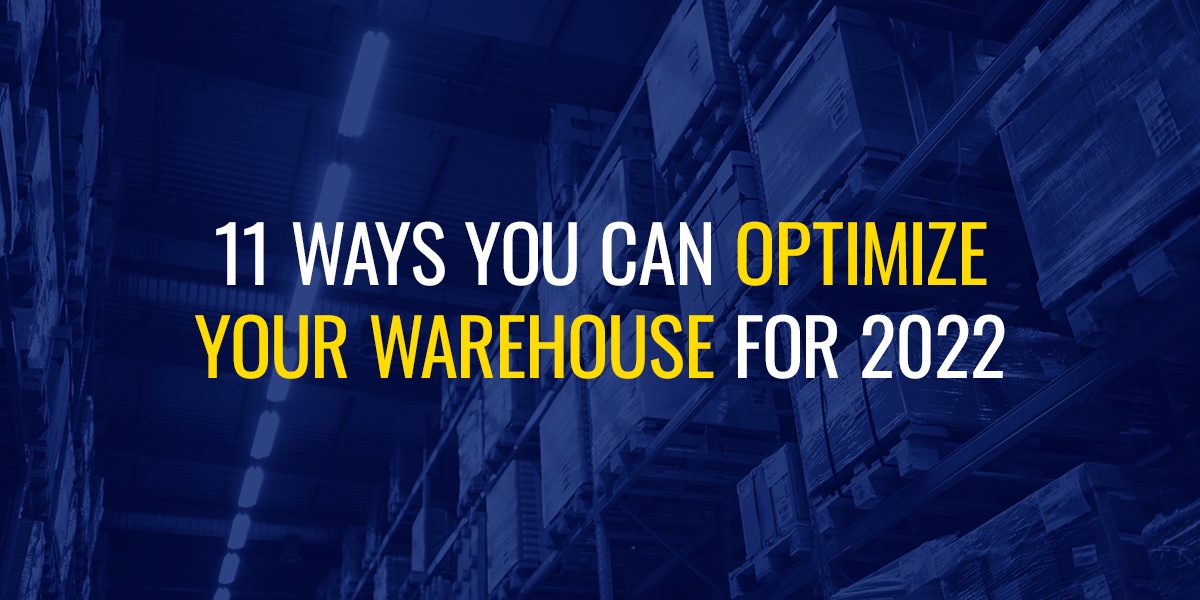
17
Nov
Your warehouse may not work as hard for you as you need it to. A poorly organized facility can lead to wasted time and squandered space, both of which can negatively affect your productivity — and your bottom line.
The recent growth of e-commerce makes having a quick, simple warehouse process more important than ever before. According to the United States Census, American e-commerce sales increased by about 3.3% in the second quarter of 2021, when adjusted for seasonal variation. This increase amounts to $222.5 billion in e-commerce sales, which is 13.3% of all retail sales in the U.S.
Improving your warehouse’s layout now will maximize productivity in the long run. Consider the following suggestions to optimize your operation for 2022.
Why Improving Warehouse Efficiency Is Essential
Warehouse optimization for increased efficiency is more crucial now than ever. U.S. retail imports have skyrocketed since the National Retail Federation began tracking them in 2002. The record-breaking amount of incoming products stems from retailers preparing for the holiday season and replenishing their depleted stocks from earlier in the year. Warehouse use will be in greater demand as these imports move through distribution centers on their way to retailers and consumers.
Well-organized and efficient warehouses can meet the increased need for higher volumes of orders from consumers and retailers alike.
Warehouse Process Improvement Tips
Managing warehouse processes improves workers’ ability to pick order components. Reducing time for picking orders and increasing the accuracy of the products pulled makes your warehouse more efficient. The following methods help improve how people interact with your warehouse and the items in it.
1. Manage Inventory Efficiently With a Cloud-Based Warehouse Management System
A warehouse management system (WMS) is a staple in today’s warehouses. The software uses information from portable barcode scanners workers wear as they pull items from shelves. The scanned details go into the system to update inventory numbers.
While not all WMS offer extra features to reduce human picking errors, some do.
A traditional onsite WMS, combined with tablets, can tell workers where to go to pull items in the warehouse. A few will even display a picture of what to pull to ensure that the worker gets the item’s correct size and count. This tech reduces the problem of a picker selecting the wrong product.
An even more intuitive solution is a WMS with cloud capabilities. Adopting a cloud-based WMS can help streamline your warehouse’s operations by reducing downtime and eliminating cybersecurity risks. With a cloud-based system, you can continue operations on any device with an internet connection, so your employees can access information while on the job and at the onsite terminal. This reduced need for hardware can shrink overhead costs and increase the visibility of your inventory in real-time.
Cloud-based WMS systems are also scalable, so you can avoid unnecessary storage costs by adjusting your storage plan to match your operation’s needs. If your warehouse’s computing needs grow, you can always add more space. And if you need to downsize, a cloud WMS can accommodate that change.
Additionally, if your warehouse processes direct-to-consumer (DTC) e-commerce, a good WMS can automatically update inventory levels on all selling platforms to prevent overselling. The retailer’s online stock levels should always match what’s going on in the warehouse, and having that information in the cloud can ensure accuracy across all channels.
Furthermore, cloud-based systems are increasing in popularity. By the end of 2021, end-user spending on public cloud software is predicted to increase by 23%, which translates to more than $330 billion in spending — up from $270 billion last year.
2. Go Digital on the Warehouse Floor
Digital tracking of order fulfillment on the warehouse floor can reduce problems by updating your centralized inventory system in real-time. Barcode scanners work well as long as each product’s labels remain on the racks and next to the correct item. However, in some instances, these labels may fall off, increasing the chances of errors in pulling goods. Tablets or mobile devices that display pictures and scan barcodes or QR codes on the racks may help avoid these issues.
Replacing paper order forms with digital barcode readers or scanners improves the accuracy of the products pulled from the shelves. Additionally, barcode readers that communicate with WMS can update the inventory based on orders pulled during the shift.
3. Track Assets With Real-Time Location System
If you want to fully upgrade your warehouse to the latest technology, consider tracking your facility’s assets with a real-time location system, or RTLS. This system combines active and passive radio frequency identification (RFID) tags, Bluetooth low-energy beacons and ultrawideband beacons. When integrated, these technologies can pinpoint the location of lift trucks and other high-cost assets in your facility within a few inches. Using RTLS is too cost-prohibitive for tracking products. But you can avoid time lost from missing or misplaced assets by using it to keep tabs on the expensive equipment in your warehouse.
Another use of RTLS and RFID technology is to use passive RFID tags, which cost much less than active models, to tag pallets. Readers at each dock can determine if a pallet arrives at the correct location for outgoing shipments.
While the investment in equipment to set up an RTLS can be high, this technology is worth considering for those who have problems with lost equipment or misdelivered loads.
4. Use Automation Where Feasible
As e-commerce grows in popularity, investing in automation like self-guided vehicles or autonomous mobile robots becomes less of a futuristic gamble. Even the most traditional warehouses are moving toward some forms of automation to speed up stocking or pulling products and save on labor.
To make a small step toward automation, consider autonomous lift trucks for moving products over long distances, such as from docks to staging areas, or making repetitive motions. Assigning monotonous or rote tasks to automated lift trucks frees your operators to handle assignments that require more experience and careful handling. Using RTLS to monitor automated lift trucks’ location ensures that you never lose vehicles and always know where they are during operation.
If you’re considering using automated machines, it might be worth looking into picking robots. With the proper attachments, they can climb shelves to pick items, stack products, attach SKU labels and more, which can speed up your process and save labor costs in the long term. While they’re still new to the scene, picking robots are sure to catch on soon.
You could also introduce automation through wearable technology like tablet-equipped wristbands or armbands. Your pickers will have hands-free, on-the-job access to inventory and order information while they work, which can help speed up the picking process and keep your employees moving.
Automation can be integrated into your WMS or other already-existing programs in your operation to further streamline your processes. Other automation developments to watch out for in 2022 include 5G connectivity, micro-fulfillment and warehouse distribution drones.
Warehouse Layout Optimization Tips
Improving warehouse layout makes workers’ jobs more straightforward, regardless of the additional equipment they use. Plus, the way you arrange the warehouse will also determine the volume of products your space can hold. With adequate planning and placement, your facility can maximize the number of products it stores.
5. Arrange Inventory Distribution Based on Demand
How you use your warehouse will help you optimize its organization. For example, warehouses that ship according to a DTC system have unique needs for fulfilling larger numbers of small orders than wholesale distributors receive. Therefore, an organization designed to speed up pickers’ ability to fill orders is even more crucial in these facilities. Rather than making room for lift trucks to pull pallets for orders, these facilities will need to separate space for lift trucks to stock racks and for pedestrian traffic to pick the orders. Using a system that allows for stocking from the rear and picking from the front can avoid collisions between trucks and pedestrians.
Facilities that fulfill large orders for retailers will need to have space for lift trucks and pallet lifts to move pallets off racks for stocking and picking. Wider aisles in front of the racks can accommodate the need for more vehicular traffic in these facilities.
In all instances, stocking sought-after products closer to the docks reduces the time spent in retrieving those goods. Rarely pulled or out-of-season items can go toward the back of the warehouse or on higher racks to free space for more in-demand goods. Optimizing a warehouse to best accommodate the type of orders it fulfills ensures that it meets everyone’s needs.
6. Don’t Overstock Rarely Requested Items
For maximum efficiency, every inch of space in your warehouse should provide a function. Don’t waste space on rarely needed items. Also, if some products go out of season, do not order more until their demand increases the next season.
If you must dedicate storage room to lower-demand items, place them in far-off corners. By placing frequently pulled items in the front, you’ll be able to make up for the additional time occasionally required to pull your low-demand stock.
7. Look Up for More Useable Space
Warehouses today typically have smaller footprints in sites for faster distribution. While roomy old-school facilities gave you the luxury of spreading out storage on low shelves or racks across the expansive space, you can’t do the same today.
Make the most of your available space by using vertical storage as much as possible. Think about installing higher racks or taller shelves to hold products that don’t have high demand. You can keep extra products on hand without needing more square footage.
If your vertical space allows, consider stacking pallets two high on the top level. This location offers an ideal place for extra stock or items that don’t sell as quickly as others. Always consult the beam and rack weight capacity to ensure they will support the double-stacked pallets. If the racks do not have the strength to accommodate the pallets, either upgrade to sturdier racks and beams or avoid double stacking on that rack.
The vertical space over dock doors can also hold spare empty boxes or cardboard. If your workers break down pallets and have extra cardboard or need a supply to assemble shipping boxes, create a storage area above the dock doors for these items. You will keep them close without taking up the precious storage space for the products in your warehouse.
8. Make Your Layout Easy to Understand
Time is valuable in a warehouse, so your pickers must be able to quickly find the products they need. However, if you have a warehouse with a confusing layout or products scattered without organization, they will take longer to pull order components. Therefore, make your warehouse layout easy for even the newest pickers to understand. One way could be to alphabetize product arrangement. Alternatively, you could install prominent labels at the ends of aisles to help your workers quickly retrieve goods.
To improve traffic flow, outline separate aisles for pedestrians and vehicles. Floor tape, guard rails or bollards can provide the needed barrier between people and trucks. For narrow aisles, mark out one-way flow patterns. Keeping people moving in the same direction in tight spaces will cut down on jams with other workers or vehicles.
Legibly label the office, storage, shipping and staging areas on the walls and floor. Paint or tape can separate these areas. However, you may also need bollards or wire partitions to keep vehicular traffic away from offices.
How to Increase Efficiency With Material Handling Equipment
The equipment used in your warehouse plays a major part in how efficiently the space operates. Combining durable, lasting racks and shelving with a well-planned layout optimizes the use of the available room that you have.
Improving a warehouse does not have to break the budget. Selecting material handling equipment specifically for the loads your warehouse handles will ensure you don’t spend too much, but still have a space that can safely hold your inventory.
9. Use Higher-Density Pallet Racking
Switching to higher-density pallet racking that stores 50% more than your old racking may double your available floor space for additional shelving, product staging or worker movement. For instance, replacing a rack with a 16,700-pound capacity for one with a 25,300-pound capacity lets you store more or heavier items on the racks, depending on their arrangement. Therefore, you can space out pallet racking in your warehouse to improve traffic flow by opening more floor space.
If your warehouse already has adequate traffic flow, using higher-density pallet racking lets you store more products or heavier loads in the same amount of space. When purchasing new pallet racking, always select models with higher capacities than you need to avoid overloading them and causing a safety hazard. If using decking on the racks, ensure the wire decks will support the same loads as the uprights.
Another way to increase pallet racking density is by adding racks and beams on lower spots for shorter items. In doing so, you can store more in the same amount of space. To avoid safety issues, make sure to never exceed the uprights’ storage capacity.
10. Facilitate Picking Individual Products With Wire Baskets
Wire baskets allow for transparent visibility of the contents while securely holding the products. For facilities that pull individual products for fulfilling consumer orders, wire baskets can make pickers’ jobs easier. With the ability to use these on the floor or on racks, baskets fit into almost any warehouse layout.
Wire baskets come in a range of sizes. Our smallest is the junior wire basket, measuring 20″ deep x 32″ wide x 22″ high. It includes a half-drop gate to ease picking when using this basket on a shelf or rack. The largest size we offer is the XL wire basket, measuring almost twice as deep and high as the junior basket.
11. Prevent Lost Products and Aisle Blockage With Rack Guards
Rack guards keep products from falling off the back of racks into aisles. Fallen products require additional time to replace and could create hazards for lift trucks driving down aisles. Plus, fragile products may sustain irreparable damage if they fall from racks. The broken items will count toward loss, as you’ll need to discard them.
Investing in rack guards protects against loss from wasted time or damaged products. They can also protect materials from getting knocked off the rack from one side. Choose a rack guard to fit the space between the uprights.
Contact T.P. Supply Co for Material Handling Solutions Today
Start the new year right by optimizing your warehouse for higher worker productivity and better profits. T.P. Supply Co is here to help make these recommendations a reality. Contact us online for racking, shelving, material handling equipment and more for your facility.