No products in the cart.
Warehouse Racking Inspection Guide
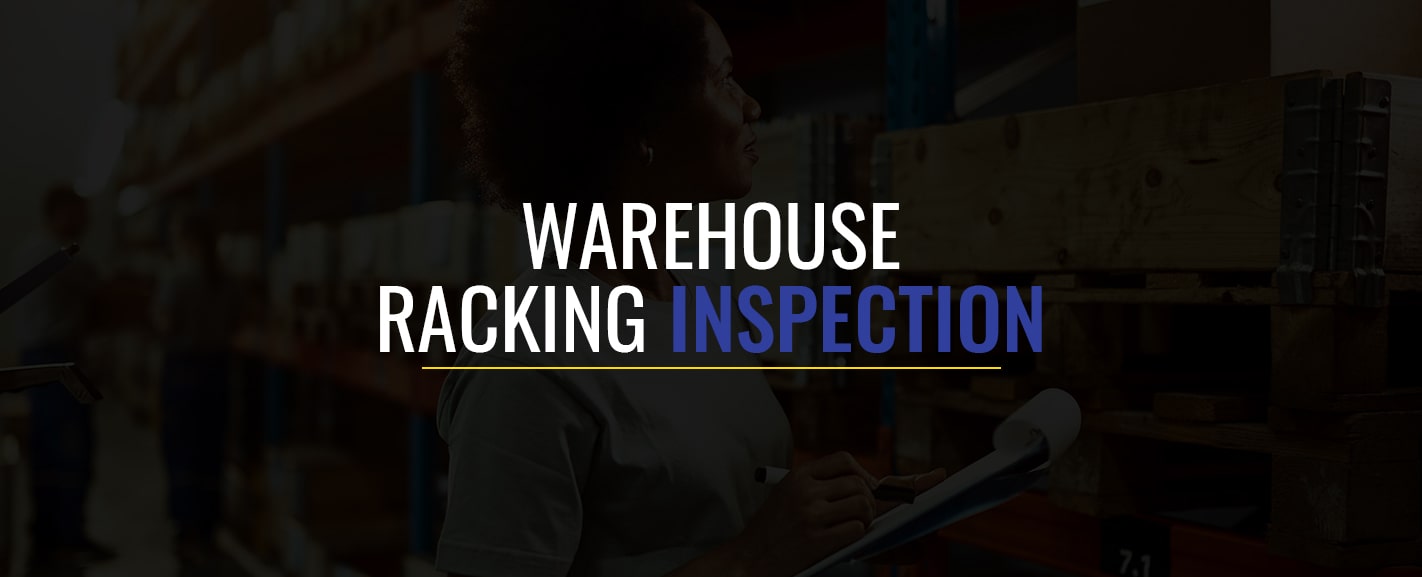
13
Jun
Warehouses are some of the busiest workplaces. Between racking, forklifts and other heavy machinery, busy staff and substantial inventory, warehouse safety is essential for efficient operations.
Pallet racking inspections are integral in achieving and maintaining warehouse standards. They aim to ensure racking systems are secure and safe to use. Effective inspections help you identify defects, damage and potential risks that can compromise the system and workplace safety.
By implementing routine racking inspections, you prioritize safety and optimize your operations. You also save revenue by avoiding unnecessary costly repairs or replacements and the associated downtime.
This warehouse racking inspection guide will give you an understanding of the guidelines and regulations regarding racking systems, provide tips for preparing for inspections and outline a checklist for comprehensive and streamlined checks.
OSHA Warehouse Racking Guidelines and Regulations
The Occupational Safety and Health Administration (OSHA) has several requirements and legal standards that warehouses must comply with to ensure worker safety and health. Although warehouse rack inspections are not mandated by OSHA — and pallet racking inspections aren’t a legal requirement for your warehouse — they are highly recommended.
What OSHA does outline are key standards and regulations for warehousing. Many of these standards are easily applicable to racking safety and inspections, as OSHA’s regulations aim to hold warehouses to the standard that workplaces should be free from recognized hazards.
Some OSHA warehouse racking regulations and materials handling and storage standards include:
- Having a well-ventilated warehouse.
- Closing off open loading dock doors and other areas where employees could potentially fall from more than 4 feet.
- Keeping the workspace free of hazards that could cause slips, trips and falls.
- Ensuring machinery is handled correctly and only employees with proper certification operate forklifts.
- Providing ongoing staff training.
- Giving staff adequate rest periods.
- Setting up your materials handling system correctly to avoid accidents.
- Storing items safely to prevent collapsing, falling and sliding.
- Marking aisles and other areas with the appropriate signage.
- Implementing effective emergency planning procedures with designated exit routes, clear protocols and tools like fire hydrants and first-aid kits.
The Benefits of Regular Pallet Rack Inspections
Conducting regular inspections can benefit your warehouse operations in various ways:
- Identifying problem areas:Â Inspections help identify and highlight any damage to the racking system. That way, you can quickly catch and address flaws before they lead to larger, more expensive issues.
- Maintaining compliance:Â Though not a legal requirement, racking inspections help ensure compliance with health and safety standards.
- Protecting revenue:Â Warehouse inspections can help protect your assets and revenue by reducing costly racking system replacements. They also help you avoid lost inventory, downtime and even possible lawsuits due to employee injuries from damaged racks.
- Gaining a competitive edge:Â A reliable racking system is key to efficient operations and client service. It helps establish you as an industry leader with whom clients want to partner.
- Optimizing storage capacity:Â Regular checks can identify flaws in your racking system and lead to improvements that enhance storage capacity and efficiency, as you can use your racking system to its full potential.
- Providing a safe working environment:Â The greatest possible benefit of conducting regular racking inspections is that it helps create a safer environment for staff. When racks are damaged and hardly checked, they could completely collapse and cause injury or worse. Pallet rack inspections help you identify and resolve potential hazards, keeping employees out of harm’s way.
- Improving appearances:Â You can build a more professional-looking warehouse when your pallet racking system is in the best condition. Damaged, corroded or dirty racks are not only potentially hazardous but make the warehouse look unkempt. Inspecting your pallet racks is an important part of maintenance that elevates your warehouse’s appearance and professionalism.
Racking Inspection Considerations and Preparations
Preparing your warehouse for pallet racking inspections starts with the basics — compiling a handy checklist. Having a checklist for your warehouse racking inspections streamlines the process and ensures more thorough checks at each assessment.
With inspection checklists, warehouse managers can rest assured that nothing important goes unassessed. Warehouse racking inspection checklists also help you standardize your operations and maintain the same quality assurance across your warehouses.
If one does find damage during the inspection, they should report it to the warehouse safety manager immediately so safety-related measures can be implemented accordingly. A comprehensive report of the issue and appropriate damage control methods are essential elements for effective reporting procedures.
A good checklist should be both comprehensive and action-orientated. The checklist should make it easy for the examiner to:
- Specify the location of any damaged racks and the degree of damage.
- Assign actions and recommendations or other notes.
- Validate the report with signatures.
To further optimize inspections and reporting, you may also consider a digital checklist. By having all your data online, you can easily track and access records and stay on top of maintenance.
Compiling a Racking Inspection Checklist
Reduced oversights and inconsistencies make compiling a pallet racking inspection guide or checklist worth it. A comprehensive check inspects all your racking systems’ individual components, including beams, braces, uprights, columns, connectors and the floor. Here are some fundamental components to include on your pallet rack inspection checklist:
1. Uprights and Columns
The uprights connect beams, while front and rear columns — which are connected with struts — form uprights. Look for the following defects when inspecting uprights:
- Rust and corrosion:Â If you have metal racking systems, rust and corrosion can gradually degrade the system to the point of collapsing. A moist or humid environment is the most likely cause of rust, but excessive contact with chemical or abrasive products can also lead to corrosion.
- Deflection:Â Deflections are significant bends in the columns that impact the structural integrity of uprights. Improper installation, overloading systems and forklift collisions can cause deflection. If left unchecked, deflection can cause racking systems to collapse under load.
- Cracks or bulges:Â Cracks and bulges can indicate poor construction, low-quality materials, forklift collision and overloading of the racking system. Cracks and bulges impact your system’s load-bearing capacity.
- Plump, level and anchored: Uprights should be vertically aligned — or plumb — to be stable and distribute the load evenly. Uprights should also be anchored securely to the floor to ensure rack stability.
2. Struts
Struts are the bracing between columns that provide stability by keeping frame posts plumb. Unfortunately, forklift collisions, corrosion and overloading pallets can damage struts. Verify that your struts:
- Are free of rust and corrosion.
- Do not deviate more than ½ inch from the horizontal or vertical plane of the frame.
3. Row Spacers
Not all racking systems use row spacers — for example, a system with a single row of pallet racks or shorter systems. For more intricate systems, row spacers help align rows and keep flue spaces (vertical lines of sight from floor to ceiling) clear. When inspecting row spacers, look for the following:
- Row spacers are installed correctly with the proper placement.
- The bottom row spacers are at least 5 inches from the ground, and the top ones are next to the highest horizontal struts.
- Row spacers are not interfering with rack beams, struts or other components.
- Row spacers are free of any defects.
- No row spacers are missing.
4. Beams
Beams connect uprights, essentially forming the shelves that support pallets and their loads. Beams provide structural support, so inspecting these elements is crucial for a sound racking system. Check for the following points during your inspection:
- Deflection: Slight deflection, or bending under the weight of a load, is normal. However, you should check beams for deflection that exceeds the recommended limit of 1/180 — or 0.55% — of the length of the beam. Typically, deflection gaps of ½ inch or greater indicate an overloaded and unsafe beam.
- Condition:Â Note any severe tears or dents in the beams, and repair or replace these components as necessary. Tears, dents, cracks and bulges usually indictae a breach in the metal surface. They often result from overloading and high-impact collisions.
- Beam connectors and supports:Â No safety pins, clips, connectors, flanges or wire decking should be missing or damaged.
5. Floors
Floors are the foundation of your racking systems and should regularly be inspected for:
- Damage to footplates, anchors and shims (components that help level uneven floors).
- Shims that are sliding out.
- Missing or loose anchors.
6. Pallets, Accessories and Overall Condition
Examining pallets, accessories and the overall condition of your pallet racking systems is key to a comprehensive checklist. Confirm the following items during your inspection:
- Pallets have no missing or broken boards.
- Load ratings are readily available to check the maximum load per level and bay.
- Pallets are in good condition without bowing, rust or rot, depending on the material.
- Accessories, such as upright guards, shrink wrap and safe working load (SWL) signage, are in optimal condition.
Conducting a Comprehensive Warehouse Racking Inspection
Your warehouse racking inspection doesn’t need to be a tedious or drawn-out process. With these pallet racking inspection tips, running regular checks can be a streamlined process:
- Include aisle and bay numbers in your report.
- Start the inspection on one end of the warehouse and work systematically to cover the entire racking system.
- Go row by row to scan the sides for signs of forklift damage or sagging beams.
- Inspect each beam and upright using a flashlight for better visibility.
- Note any form of damage or concern, whether the issue was part of your safety checklist or not.
- Submit reports on time and maintain an efficient follow-up procedure.
Maintenance Best Practices
Racking inspections are one part of maintaining your system. Implementing maintenance best practices helps extend the longevity of your racking system and streamline processes. Most importantly, maintenance helps prevent racking damage and gives you a clear indication of when to repair or upgrade your racking system.
Maintenance best practices include:
- Performing comprehensive pallet racking inspections.
- Adding safety products to your racking system, including column guards, aisle guards, guardrails and safety gates.
- Regularly training staff not to overload the system.
- Regularly training forklift operators.
- Implementing layout and design changes to overcome problem areas, such as those with frequent collisions.
No matter how careful staff members are, your racking system will eventually need repairs or upgrades. If individual components are damaged or missing, repairs are a cost-effective way to maintain your system. But if the damage is severe enough to compromise your racking system’s structural integrity, it’s better to upgrade your system for full compliance, efficiency and safety.
You may also upgrade your system if your warehouse is growing, a previous installation wasn’t up to standards or your current layout no longer suits your needs or preferences. At T.P. Supply Company, Inc., you can enjoy a variety of options on new or used pallet racking equipment. We can help you find solutions that suit your pallet racking system budget and needs.
FAQs on Warehouse Racking Inspection
There are various elements to consider when designing a racking inspection process for your warehouse. The answers to these frequently asked questions can help you put the pieces together:
1. How Frequently Should Heavily Used Racks Be Inspected?
OHSA does not have specific compliance guidelines for warehouse racking inspections and how often you should conduct them, but the United Kingdom Health and Safety Executive recommends racking inspections at least once every 12 months.
If your warehouse is particularly busy, you may even conduct more regular inspections every six months or every quarter. You should also conduct a safety check after any changes to your racking system, including installations, upgrades, replacements and modifications.
2. What Happens if Warehouses Don’t Conduct Regular Pallet Rack Inspections?
Without regular inspections, you risk the integrity of your racking systems. Systems can collapse due to unchecked damage, leading to safety hazards, potential lawsuits and the costs of product loss and downtime.
By keeping up with regular checks, repairs and maintenance, you can minimize costly damages, create a safer workplace for personnel and uphold a positive business reputation.
3. How Can You Prevent Pallet Racking Damage?
There are several ways to keep your pallet racking system in good condition, including:
- Training staff on best practices to prevent pallet rack overloading and forklift collisions.
- Conducting regular inspections and maintenance.
- Creating an effective layout throughout your warehouse with the correct spacing and signage.
- Repairing or replacing damaged parts efficiently so your racking system doesn’t experience further damage.
By following these protocols, you can ensure a durable, reliable and long-lasting pallet racking system for your warehouse and staff.
Contact T.P. Supply Company, Inc. for Warehouse Racking Solutions Today
Setting up regular inspections for your warehouse’s racking system is nonnegotiable. Regular checks help keep your operations compliant by elevating safety standards and professionalism in the warehouse.
At T.P. Supply Company, Inc., we can partner with your business to provide effective storage and shelving solutions, including safety and security products that contribute to strong racking systems. Among our selection of quality pallet racking products and services, we offer aisle protection, guard rails, machine guarding, wire partitions and bollards.
T.P. Supply Company, Inc. offers the full package, from customized quotes on industrial pallet racks to professional advice, delivery and installations. We also have a reliable in-house team that completes deliveries and installations. Find the right shelving solutions for your business today by contacting us online or calling 877-302-2337 with any questions!