No products in the cart.
Beginner’s Guide to Pallet Racking
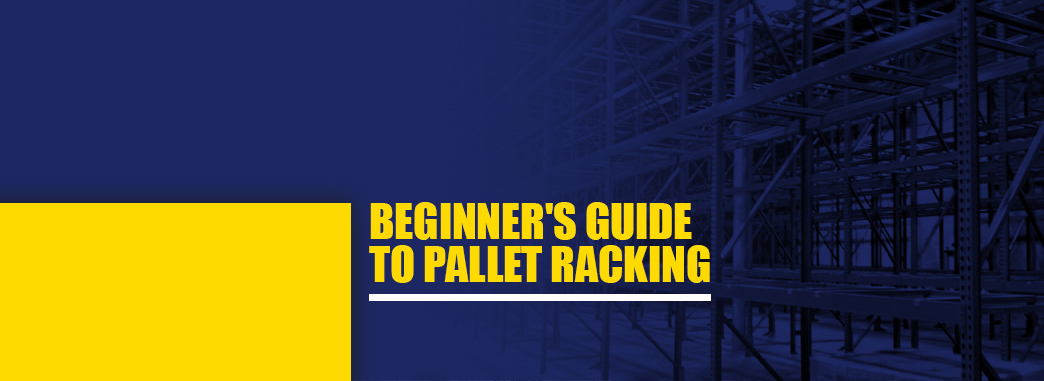
15
Feb
If your warehouse is like most, you keep stock organized on pallet racking. With so many pallet rack sizes and types, narrowing down your options may seem overwhelming. However, you can find the best pallet racks for your facility’s needs by looking at what materials you stock and how you need to access them. Continue reading our pallet racking guide to learn more about what solutions are best for your warehouse.
Why You Need Pallet Racks
Pallets hold loads of goods in a warehouse or other storage facility. The design of the pallets makes it easier to move the goods on them with a forklift. To preserve what you have stored on the pallet from pests and moisture, you should not keep the pallets directly on the floor. Floor storage puts the goods at risk of damage while making it harder to move them when needed.
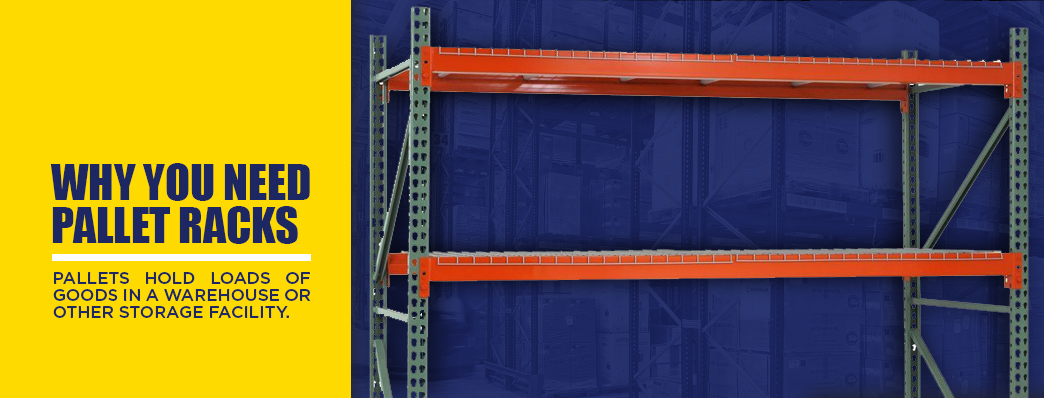
A well-organized warehouse is much more productive than one that lacks arrangement. Pallet racks help you keep goods stored in easy-to-find spots while reducing floor space. Your workers can move around the facility faster and retrieve pallets quicker if you have an adequate storage system. The pallet racks you use for storing inventory make the difference.
Though you may already know why you need pallet racks, you may not be aware of the many types of systems available. Depending on how you arrange goods in your warehouse, you have several choices of racking systems.
Different Types of Pallet Racking
With storage systems, you have multiple options to suit your warehouse’s operations. How you stock and pull inventory will significantly determine the type of pallet racks you need. Some are more common than others, based on the most frequently used pick and pull systems. Learn the different rack options available to make choosing the right ones for your facility easier.
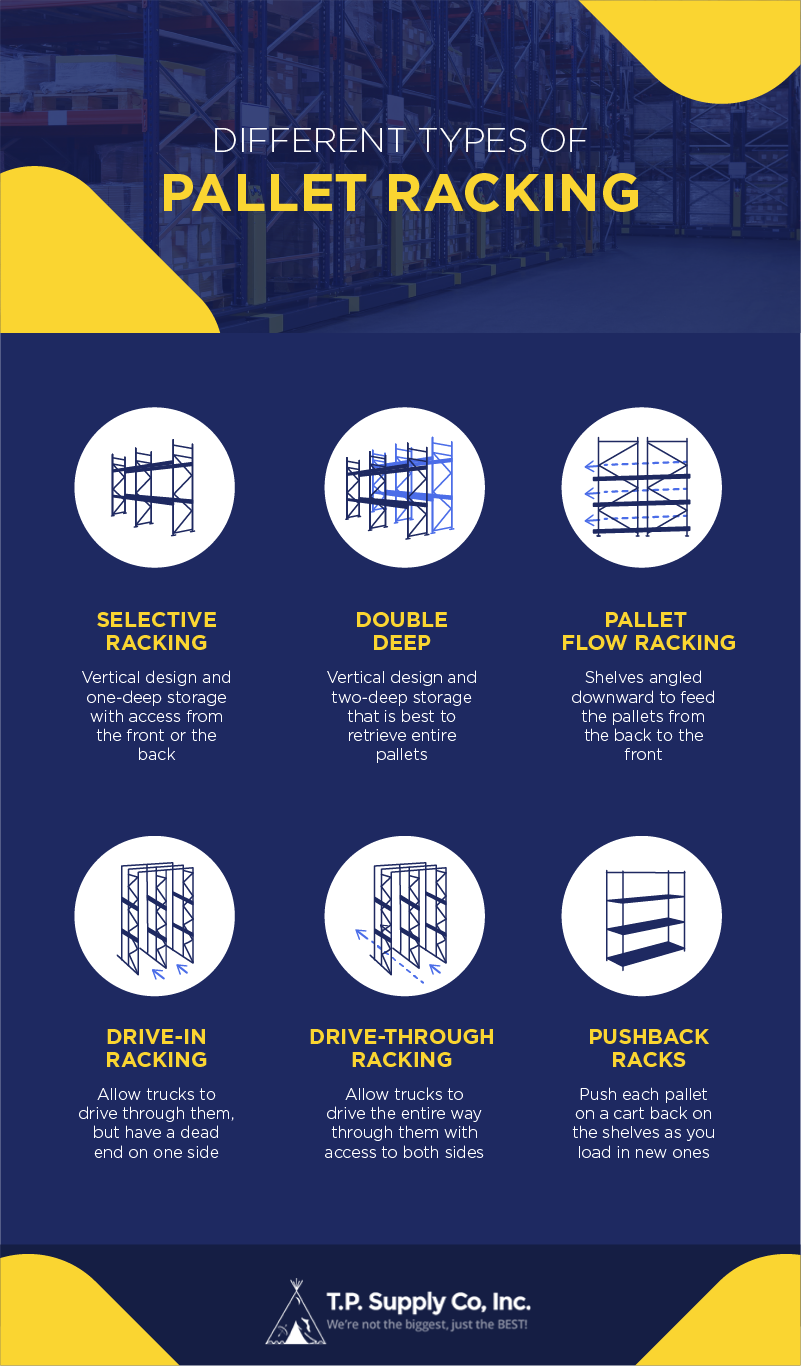
1. Selective Racking
Selective racking ranks as the most common type of system. Due to its vertical design and one-deep storage, you can use a majority of the space for storage. This system is best for first in-first out storing and retrieval. It also provides access to all pallets in stock by picking from the front or back of the shelves. Additionally, this form of racking allows for increased flexibility because you can add wire decking to allow for storing products off pallets, as well. Unfortunately, since you cannot have shelves as wide as with other storage methods, you will need more single-deep selective racks in your facility than different types of systems.
2. Double Deep
Selective racking may be single-deep or double-deep. For a high-density storage system for first in-last out retrieval, consider double deep racking. Use this system if you retrieve entire pallets for orders rather than pulling inventory off pallets. Compared to other forms of high-density storage, double deep racking costs less and lets you use the most the shelving space. If you stack the pallets high, your lifts may need cameras and extended reach to get your operators to the higher levels. Even without extra-tall racks, to reach the rear pallets, you will need a means of extending the reach of your lift truck.
3. Pallet Flow Racking
If you store large numbers of pallets carrying the same goods, consider a pallet flow system, also called a gravity flow system. These racks angle the shelves downward to automatically feed the next pallet into the front of the shelf for picking. If you use a first in-first out system, pallet flow racking is ideal since the order you feed the pallets into the system from the back of the shelves is the same as the order you will pick them in from the front of the shelves. Depending on the size of the racks you purchase, you could stack pallets up to 20 deep.
4. Drive-In Racking
When you have shelving that allows trucks to drive through them, you have a drive-in, also known as a drive-through, system. Use this system for storing large amounts of inventory in a compact space. The design of pallet racks and shelves allow you to stack pallets up to seven high and 12 deep. Though this system provides for storing almost twice as much as a selective racking system, you only will have up to 60 percent use. The method best for drive-in racking is last in-first out. Despite its benefits, this racking system has some downsides. The care required by the lift truck driver may slow the rate of picking and storage. Additionally, you can only store products with overall uniform sizes on the pallets.
5. Drive-Through Racking
Drive-through racks have a similar design to drive-in systems, but you can drive a lift truck all the way through the tunnel, whereas drive-in systems have a dead-end in them. Since you can access both sides, this system allows for first in-first out methods.
6. Pushback Racks
If you implement a first in-last out system, consider pushback racking. This system pushes each pallet on a cart back on the shelves as you load in new ones. Though you can have these racks filled up to six-deep, most warehouse operators opt for only two deep. Unlike other systems, you cannot store partially filled pallets on a pushback system. Though you can use almost all of the available space, these racks can cause damage to pallets that should not touch each other.
Choosing the Right Pallet Racking System
Depending on your operations, you may find one pallet system more beneficial to your warehouse’s needs than another. Several factors will play into helping you make the right choice for your storage facility.
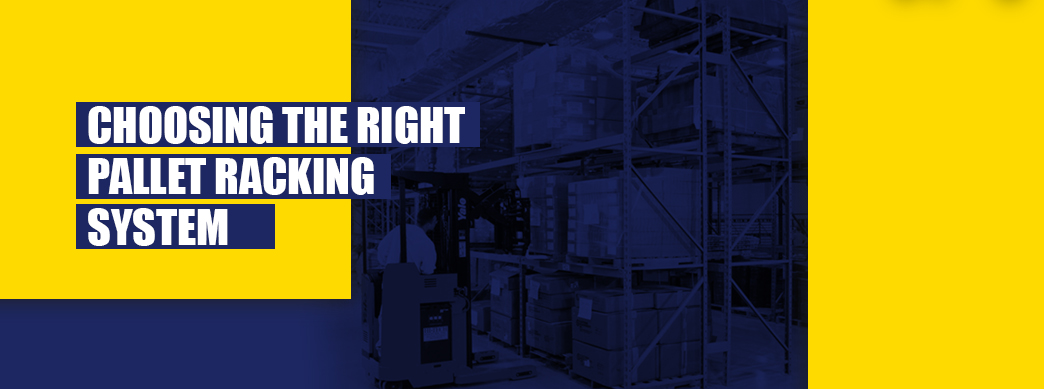
- Storage method:Â Do you use first in-last out or first in-first out systems? The answer will narrow down the racking systems available to you. For first in-last out options, pushback racks are a good choice. Racking options for first in-first out include drive-in, pallet flow and selective racking.
- Moving equipment:Â Do you have equipment available to reach shelves above standard height? You may not be able to stack pallets several shelves high if you do not also have the retrieval equipment to safely and quickly remove them.
- Space available:Â How much space do you have for racks? Will racks that require aisles in the front and back fit into your warehouse? Do you need a system that only requires access from the front? If you want to install as many shelves as possible in your warehouse, reduce the number of aisles you have by selecting racking systems that load and pull from the front only.
- Type of storage:Â Do you need to break up pallets to retrieve inventory from them? You may not be able to use double deep or other high-capacity storage systems if you regularly need partial pallets.
- Inventory stored:Â The type and weight of the inventory you store will help you choose the load capacity of the pallet racking system you need. The sizes of the pallets will also help you find the right size uprights and beams.
- Storage use:Â Not all racking systems allow you to use every inch of storage space. Some types have greater space use than others. Drive-in racking, while convenient, does not allow for using as much use of the storage space as selective racking.
- Inventory type:Â Do you have multiple product types you store? Or is your warehouse filled with a smaller variety of products kept in large volumes? You may benefit from a double deep storage method if your facility houses considerable quantities of the same product. However, consider a single-deep storage option if you keep a wider variety of items on hand.
- Location:Â One other factor you should consider when choosing racking systems is your location. If you are in an earthquake-prone area, you may need stronger racks to prevent product loss or injury if an earthquake occurs.
Racking Systems for the Future
A racking system is an investment, and you will want the type you choose to serve you today and tomorrow. Future changes in the warehouse and distribution industries will require faster picking times. By 2028, predictions from industry leaders suggest 40 percent of products will ship in two hours or less. How will your facility prepare for this scenario in under a decade? The pallet racking system you choose may have a role in your facility’s preparedness.
Though pallet racks have mainly remained the same over the years, their uses and placement in facilities have changed to allow for automated storage and retrieval systems or to reduce the picking time. Will the system you install now be capable of handling the substantial needs of future delivery times?
Determining the Sizes of Pallet Rack Uprights and Beams
One of the most critical attributes of creating a racking system is the size of the components. You need to select the uprights and beams that will accommodate the size and number of pallets you want to store. Getting the right size of these parts is even more important than knowing how to build pallet racking because you can have the racks professionally installed.
Determine the pallet sizes and how many you will have per shelf. Measure your pallets and the heights of the loads you store on them. When considering height between beams, add at least 6 inches above the tallest products you will store. Also, allow for storage on all sides around the pallets when calculating the depth. If you have a system that will enable stacking pallets, consider that when choosing the height for the uprights.
Typical pallet rack bays measure 96 inches wide and 42 to 44 inches deep. These measurements accommodate two standard pallets. You may need larger rack bays for storing more pallets. Pallet racking sizes also depend on the type of storage racks you use. Gravity flow racks do not require space between pallets, which is why you should not use flow racking for pallets with easily damaged contents.
For example, in a facility with an automated storage and retrieval system, uprights could reach 125 feet tall. Unlike racking systems of the past, which once averaged 20 feet tall, today’s systems average between 40 and 50 feet in height. With so many differences in the heights of the uprights, you may need help finding the right size racking components. We’re here to help you find the right sizes for your shelving system.
If you need help determining the measurements for your pallet racking system, contact us at T.P. Supply Co. We can help you find the right size uprights and beams for your needs. The exact measurements will depend on the type of system you use and the amount of space you need between pallets.
The Capacity of Pallet Racking Systems
The capacity of your system is how much the system can hold. Upright and beam heights both control the maximum weight your pallet racking system will support. Individual pallets may support up to 3,500 pounds each. The number of pallets you have will help you decide on the capacity of the rack. However, do not purchase storage systems that will accommodate a weight equal to what you will store. Always incorporate extra weight to prevent the racking system from collapsing.
Pallet Racking Installation Guide
How you install a pallet racking system depends on the type you purchased. Some installation and fitting methods are used more frequently in some parts of the world than in others, though you can find all types worldwide. The two primary methods are welding or bolting together the upright frame parts. In European warehouses, bolting is the preferred method, but in American facilities, most choose to weld the vertical pieces.
As with the upright frames, you have options for connecting the beams and frames. Some systems require bolting while others use a slotted system to connect the parts. Check with the manufacturer of your racking system to see which method they recommend.
Installing racking systems requires time and personnel you may not have available. If you want to ensure you have adequately installed storage racks, book our professional installation service. With professional installation, you will not have to worry about whether you put the racking system together correctly. Because the safety of your employees and the security of your inventory are at stake, how tightly put together your racking system is does make a difference in your operations.
Contact T.P. Supply Co for Pallet Racking and Installation
Whether you need to expand the storage space you have, replace aging racks or create a new storage area from scratch, let us at T.P. Supply Co help with your endeavor. While we are not the largest provider of warehouse supplies, we strive to be the best by offering parts directly to you. Since we don’t contract out our work, we can ensure you the best service possible.
When you order pallet rack systems from us, you have the choice of new, used or reconditioned pallet racking parts to match your budget. We have in-house drivers and installers to make coordinating your installation much more manageable. From brand-name racks to individual parts and refurbished frames, you can find everything you need in our online store. Check out our range of pallet rack types and accessories to locate the right ones for your warehouse. If you need to customize your order, we can also help you with that through our easy-to-use customized quote tool. Contact us today for the pallet racking system your warehouse needs to maximize its storage capabilities.
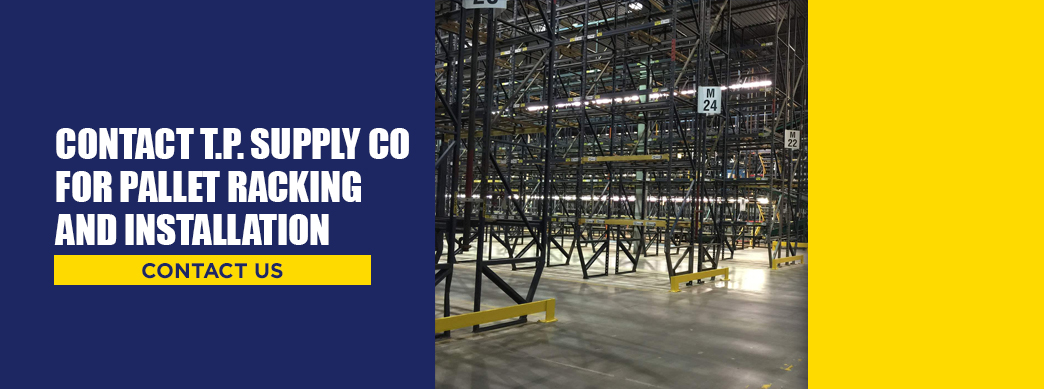