No products in the cart.
How to Calculate Warehouse Space and Storage Capacity
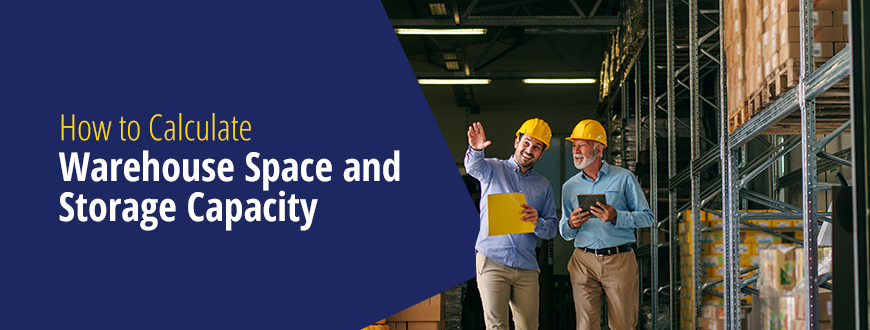
28
Aug
In warehouses and other storage facilities, space is arguably the most valuable asset. By making the best use of their warehouse space, businesses can significantly increase the amount of product they can store in the facility. By being able to store more items at once, they can save money on transportation costs and other expenses. Plus, it allows the staff better access to products, thus allowing them to fulfill orders faster and ultimately get products to the customer sooner. Because of how precious space is in a warehouse setting, warehouse managers and business owners should take the time to calculate how much space they have and how well they’re utilizing it. In this article, we’ll discuss how to make those calculations and improve how you’re using your warehouse’s available storage space.
Factors to Consider When Calculating Warehouse Space Requirements
When calculating the amount of space you need in a warehouse, consider these factors:Â
- Pallet size: Pallets come in various sizes, which can have an impact on the amount of room your inventory will take up in the warehouse.Â
- Number of pallets: Knowing the number of pallets you will be storing will be crucial when calculating your warehouse’s storage capacity. If you don’t have an exact number, you can use an estimate.Â
- Stack height: One way to make the most of your space is by stacking your pallets on top of each other. For this method, you will need to know the recommended stacking height to prevent your stacks from toppling over or being a safety hazard. The stacking height will depend on the pallet weight, the materials being stored and the pallet size.Â
- Warehouse space utilization: Your warehouse layout and how you place your inventory also impact your required storage space. For effective warehouse space utilization and streamlined operations, implement a floor plan that separates storage space, loading and unloading areas and shipping bays.
Calculating Your Warehouse’s Total Storage Capacity of Your Warehouse
To figure out how well you’re using your warehouse storage space, you first need to calculate the total storage capacity of the building. A common mistake is merely calculating the square footage of the entire facility and leaving it at that. This number, however, does not account for space within the building that cannot be used for product storage. For this reason, you have to take a few additional steps to reach an accurate number for your warehouse’s total storage capacity. Follow these four steps:
- Calculate the complete square footage of your warehouse. Let’s say it’s 100,000 square feet.
- Subtract the total average square footage of warehouse space used for non-storage purposes. This should include any office space, bathrooms, loading areas and other space where you cannot store goods. Let’s say that calculation comes out to 20,000 square feet. So, your warehouse has 80,000 square feet of usable space.
- Determine your building’s clear height, which is the distance from the floor to an overhead object. For most buildings, this would be the distance from the floor to the facility’s steel shell, but it could also be the distance from the floor to the lowest-hanging overhead objects, such as lighting or equipment. Your building’s clear height will impact your usable space because it dictates how high up you can store items.
- To find the total storage capacity of the warehouse in cubic feet, multiply the facility’s clear height by your total square footage of usable space, which is 80,000 square feet in this case. From our example above, the clear height of the building is 25 feet, and the warehouse has a total storage capacity of 2,000,000 cubic feet.
The reason you must convert your warehouse’s total storage capacity into cubic feet is because it makes it easier to analyze how well you’re using that space, as you can also calculate your warehouse storage utilization in terms of cubic feet.
Are You Utilizing All of Your Warehouse Space?
Once you know the total storage capacity of your warehouse space, you can begin to analyze how well you are utilizing that space. You can do this in two steps: learning how to calculate warehouse space utilization and then analyzing your individual usage.
1. Learn How to Calculate Warehouse Space Utilization
Calculating your warehouse space utilization will help you make sure you’re as efficient as possible with the available space at your facility. This number represents the percentage of your usable storage space that you’re using. Believe it or not, you don’t want this number to be a perfect 100% — in fact, you want it to be much lower than that. We’ll explain why after going over the calculation. Going back to our previous example, we know the total storage capacity of the warehouse is 2,000,000 cubic feet. To determine how much of that space you’re actually using, you’ll need to calculate the inventory cube size of your facility. Follow these steps to calculate the inventory cube size of your warehouse:
- Measure the footprints of all your pallet racks.
- Calculate their total vertical storage capacity.
- Multiply the true capacity of each of the pallet racks in your warehouse by the total number of racks you have.
The number you reach after making those calculations represents the size of your warehouse’s storage cube. Let’s say the number you landed on after doing this math is 500,000. With your total storage space measure being 2,000,000, that means your storage utilization percentage would be 25% — which is pretty good.
2. Start Evaluating Your Warehouse Space Utilization
Some of you may be wondering: “Why is 25% a good utilization percentage? Shouldn’t it be closer to full capacity?” The short answer is no. Instead, having a storage utilization that is more than 27% or less than 22% would signal a potential issue in the layout and design of your warehouse. A utilization percentage of more than 27% would likely mean your staff is having a difficult time moving around the warehouse to pick and restock items, which would result in high labor expenses.
On the other hand, a storage cube size that is less than 22% of your facility’s total storage capacity would indicate that you may be wasting potential storage space due to the layout of your warehouse. If we’re still working with the warehouse that has 2,000,000 cubic feet of usable storage space, that would mean a storage cube of between 440,000 and 540,000 would be ideal.
So, let’s take the middle of that range — 490,000 — and say that’s the storage cube size to aim for to achieve the optimal warehouse storage efficiency. This number, of course, will vary for every warehouse.
But for the sake of this example, let’s say this particular warehouse has a 490,000 storage cube size. Warehouse managers and designers can then lay out the facility with optimization and efficiency in mind, and you can calculate how much of that storage cube size you are actually utilizing. If you are storing 350,000 of product, you would be using 71.42% of the optimal storage space that is available.
3. Make Changes to Optimize Warehouse Capacity
After analyzing your warehouse space utilization and identifying areas for improvement, it’s time to implement changes. This process may involve several strategies, and the best approach will depend on your specific situation and average warehouse size.Â
One common tactic is to reconfigure your warehouse layout. You can adjust aisle widths to accommodate more inventory or switch to a different racking system that allows for more compact storage. Consider vertical space as well. Can you use higher shelving or implement a mezzanine system to increase your storage capacity? Â
Another key area to examine is your inventory management practices. Check whether you are holding onto any obsolete or slow-moving stock that is taking up valuable space. Implement a system for regularly reviewing your inventory and identifying items that need to be sold, recycled or discarded.Â
Optimizing your picking and packing processes can also contribute to better space utilization. Using technology like barcode scanners or warehouse management systems (WMS) can reduce the time spent searching for items and improve overall efficiency. A WMS can also provide valuable data on inventory levels, movement and storage locations, helping you make informed decisions about space allocation.
Contact T.P. Supply Company, Inc. to Get Everything You Need!
Once you have calculated what you need in your warehouse, contact T.P. Supply Company, Inc. by filling out our online form or give us a quick call if you have any questions or need to order supplies for your warehouse! If you want more information on how to maximize your warehouse capacity, click here!