No products in the cart.
Using Minimum Warehouse Aisle Widths to Maximize Space
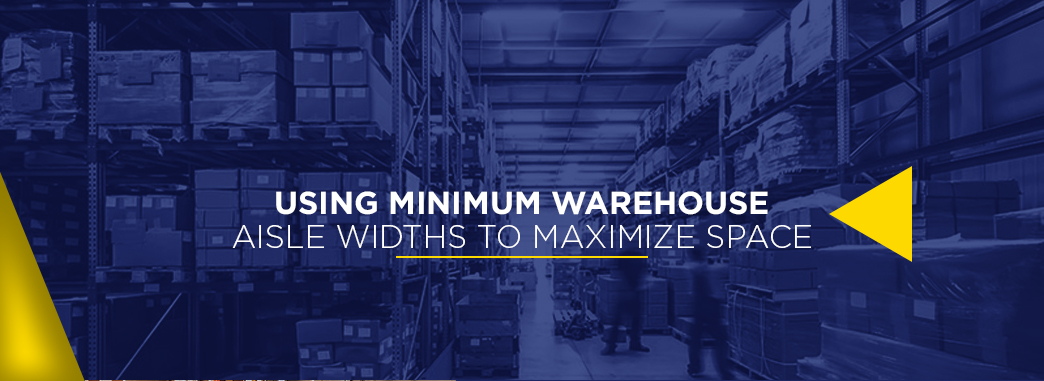
23
Apr
With today’s real estate prices in the warehouse market, you must take advantage of all the useable space you have. While there’s plenty of good advice about making the most of vertical space by filling your racks to the roof, there is another way to maximize warehouse space. An often overlooked warehouse design practice is to make the most of your warehouse aisle widths.
If you’re wondering how wide your warehouse aisles should be, there are several important factors to consider. Minimum aisle widths in a warehouse aren’t an exact measurement. Warehouse aisle width requirements largely depend on the type of material handling equipment you use.
Determining the minimum aisle width for a forklift relies on the forklift model and configuration. Forklift types have a significant impact on designing your optimum distance between pallet racking and industrial shelving. You can follow specific rules of thumb that indicate just how much space a particular forklift needs to operate safely and efficiently.
Reducing Aisle Width to Maximize Warehouse Space
Studies by supply chain consultants strive to help warehouse managers and operators like you squeeze every available square foot to maximize valuable floor space. Experts realize many warehouse operations fail to look at their cubic foot area as an integral part of the storage equation. Although warehouse values get calculated on a cost-per-square-foot formula, failure to think upward means leaving a lot of money on the table.
Smart operators realize the value in stacking products as high as they can. But even the thriftiest managers sometimes forget reducing aisle width to maximize warehouse space is another valuable key to efficiency. However, it’s easier to talk about than it is to enact, and sometimes this strategy can work against you.
Professional warehouse designers believe once a warehouse achieves between 80 and 85 percent of filled floor space, it’s reached maximum efficiency. Capacity above this becomes counterproductive when you don’t have enough area to safely and smoothly pick and place products. That is why the very narrow aisle warehouse layout concept has gained in popularity.
It makes sense to reduce your warehouse aisle widths to free up more useable floor and vertical space. Warehouse designers work with these three aisle concepts and widths.
- Wide aisle design: This is the typical warehouse design that’s been around for ages. The wide aisle concept evolved due to the available material handling equipment of the time. These were conventional counterbalanced forklifts needing about 12 feet of aisle width to function. With tighter spaces, there wasn’t enough aisle space to accommodate a forklift’s body length, its load size and a reasonable amount of clearance for safe turning.
- Narrow aisle design: As forklift designs evolved, they required less area for maneuvering in warehouse aisles. Design improvements happened partly because technology advancements made them more efficient in compact configurations. Forklifts also became smaller because of economics. Increasing floor space costs demanded improvements in area capitalization. As such, aisle widths reduced to meet compact lift sizes, which were about eight feet.
- Very narrow aisle designs: This next generation of aisle width design is catching on in new warehouse construction. Some companies are even renovating their older and existing warehouse facilities to meet the very narrow aisle layout. These aisles are size-reduced to less than six feet. That might seem like tight quarters, but modern forklifts made for very narrow aisle applications make out just fine. Very narrow aisle designs aren’t the wave of the future. They’re here to stay, and they are highly effective in maximizing your warehouse space.