No products in the cart.
Top 10 Warehouse Safety Tips
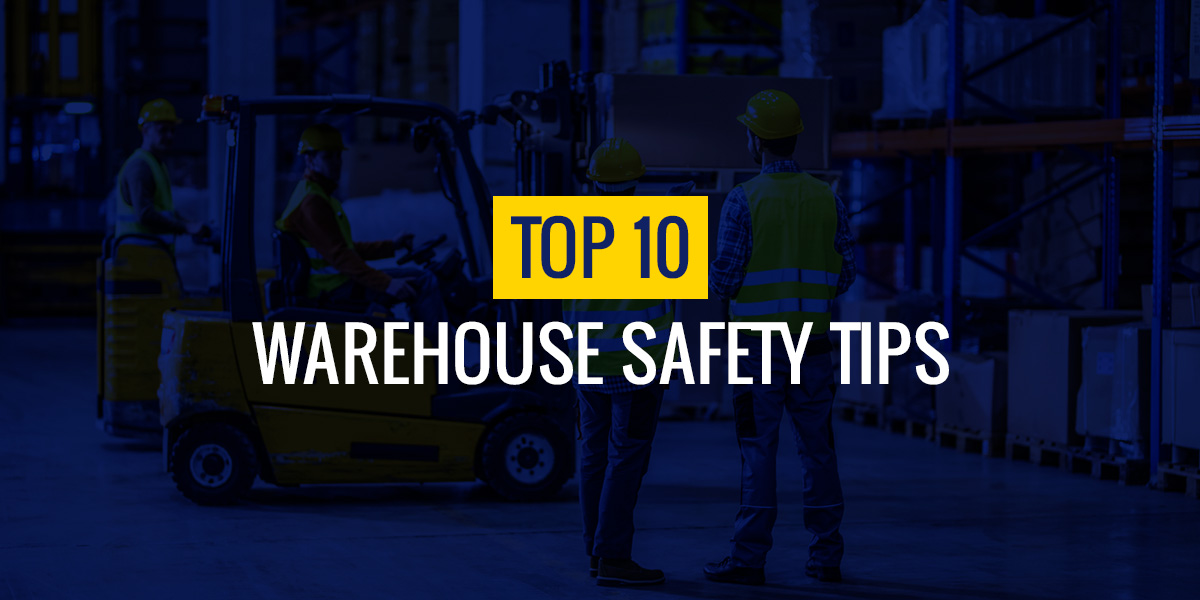
23
Nov
Employee well-being is your top concern, and prioritizing warehouse safety is one way to enhance productivity and minimize hazards. You can create a safer workspace and avoid warehouse injuries with the right practices and preemptive measures.
Why Is Safety So Important in a Warehouse?
Warehouse safety is vital for preventing accidents and injuries, and every worksite has its own risks. For example, warehouses can store hazardous chemicals that can spill and cause harm. Warehouses may have slip, fall, air contamination and machinery dangers. Workers must pack and move inventory, operate machines and load warehouse containers.
Warehouse tasks can compromise workers’ safety and lead to nonfatal and fatal accidents. In 2021, there were 253,100 cases in the transportation and warehousing sector, an increase from 2020.
For example, if containers or heavy loads are not stored and packed correctly, they can fall, injuring many employees. Forklift accidents are among the most significant warehouse injuries affecting workers.
With the increase in warehouse injuries, the occupational safety and health administration (OSHA) is enhancing regulations on logging and submitting injuries on duty.
Reporting warehouse incidents is one of many ways to reduce work injuries. Following other safety measures like wearing protective equipment (PPE), equipment inspections, first-aid training, designating hazard zones and training staff on safety can help prevent injury and fatality. It can also reduce production lulls and downtime.
A safe working environment can also increase employee engagement and satisfaction, leading to a more motivated and happy workforce.
10 Warehouse Safety Tips
Warehouse safety includes tracking injury incidents, teaching emergency protocols, marking hazard-free workspaces and installing safety supplies. You can mitigate various work site injuries and lawsuits with detailed safety guidelines and instructions.
Keeping your team updated with the latest safety tips and encouraging them to ask questions on warehouse safety protocols is one of the best ways to ensure everyone has the tools they need to protect themselves. Here are some additional safety tips for warehouse workers:
1. Provide Protective Equipment
Protecting your staff involves providing PPE like masks, goggles, steel-toe boots, safety suits and gloves. Your employees can protect their eyes, ears, lungs and other areas with adequate safety gear. PPE can protect workers in many ways:
- Protective suits and boots: Coveralls and chemical-resistant clothing help prevent exposure to hazardous materials like acids, pesticides, gases and glues and flammable liquids.
- Sturdy, no-slip shoes:Â Steel-toe shoes or boots help reduce crushing injuries, such as a box or another heavy object landing on someone’s foot. The footwear should also have an excellent grip to minimize the risk of an employee slipping and falling.
- Ear protection:Â Mitigate ear damage with hearing devices to minimize extreme noise.
- Eyewear:Â Protective glasses, face shields and goggles can shield eyes from debris and harmful particles and gasses like sulfur dioxide and nitrogen dioxide.
- Hooded chemical-resistant clothing:Â Aprons, sleeves and coveralls can help prevent burns and other harm.
- Headgear:Â Hard hats and welding helmets can protect workers from falling objects and head injuries when driving machines and prevent sparks from harming the eyes and head while welding.
- Gloves:Â Sturdy gloves help protect against cuts and scratches. In colder conditions, they also provide warmth.
- Respiratory breathing devices:Â Face shields and entire piece berthing apparatus and masks can prevent workers from breathing in harmful chemicals with covers and other repository devices. Masks can also control the spreading of illnesses.
- Safety vests: Bright yellow safety vests and jackets make it easier for workers to see each other, reducing the risk of injury.
2. Optimize Warehouse Layout
Sensibly arranging your warehouse and increasing efficiency also helps reduce workplace injuries. For example, keeping the most popular items near the packing station minimizes the need for an employee or forklift to travel great distances to retrieve those items.
Having clearly defined work areas reduces the chance that an object will get placed outside a room, where workers can trip over it. Putting boxes to be unpacked near the dumpster or trash makes it more likely that packaging will get thrown out immediately rather than left on the floor.
Installing fans and air vents near forklifts and other machinery can prevent fumes like carbon monoxide from lingering and affecting indoor air quality and working conditions. Consider installing light and HVAC systems near workstations to help regulate temperature and provide excellent lighting.
3. Train Staff Early and Often
Every person working in a warehouse should know what their job is and perform it correctly. When you hire employees, provide them with training so everyone is on the same page about job requirements. It’s also a good idea to provide ongoing training so that people learn new skills. Ongoing training also helps you verify that workers know how to do their jobs well.
With forklift operations, it’s vital to have strict rules regarding who can drive the equipment. Forklift operators need adequate training. Ideally, they’ll complete a program that provides them with a certificate to show their competency. Only allow people 18 and over to operate a forklift if they meet the appropriate training program.
Implementing rules and guidelines on packing, stacking, storing and loading products can also help workers prioritize safe methods. You can educate staff on operational strategies to improve coordination and communication.
4. Inspect Equipment Frequently
Warehouse equipment, such as conveyor belts, forklifts and racks, can wear out with time and use and become unstable or unsafe. Perform regular equipment inspections to ensure it is still operating as it should.
Ideally, inspections will occur at the start of each shift. Workers should verify the equipment is in good working order before they start the workday. It’s also essential to perform more in-depth maintenance inspections monthly or quarterly. Inspections can include:
- Identifying if tools are working before use.
- Assessing equipment safety mechanisms.
- Repairing and replacing faulty or damaged tools.
5. Keep Paths Clear
Packages and supplies spilling into aisles create a trip-and-fall hazard. Make sure everything gets put away in its proper place when people aren’t using it. There should be designated areas to place items when they are in use, such as a table or on a clearly labeled portion of the floor.
To reduce the chance of collisions when people are driving forklifts or other machinery, use arrow markings to show which direction the machinery should travel in. You might also want to mark out lanes — one for machinery and one for people on foot. Here are some ways to keep paths free from obstructions:
- Clean any spills and leaks as they happen.
- Keep workstations uncluttered and organized.
- Put waste and other objects in a designated area.
6. Stack and Store Inventory Properly
Keep heavier items on the lower shelves of storage racks to make it easier to move and retrieve them. Also, be aware of the weight limits of the racks you use and avoid putting more than the maximum weight on each one.
7. Install Guardrails and Shields
Guardrails can keep people from falling into openings on the floor or off the side of the loading dock. You can also install barrier rails to keep workers away from specific equipment.
To minimize the risk of objects falling from racks or shelves, install shields on the ends of aisles and rack guards to keep products from falling from the backside of the rack.
8. Label and Identify Hazard Areas
Labels and pictograms indicating hazardous chemicals or obstructions can improve safety in warehouses. You can place signage in visible areas so workers know about any hazards. Signage can include pictograms and labels on flammable materials, skin irritants and toxic substances. They can also indicate keeping lanes clear to prevent forklift and other machinery accidents.
Here are some more examples of signage you can implement:
- Danger signs:Â Shows flammable materials like gas and cautions against skin corrosion, burns and eye damage.
- Warning signs:Â Indicates gasses and chemicals and cautions against respiratory, skin and irritants.
- Health hazards signs:Â Indicates toxic air contaminants and can caution against fatal or harmful effects.
- Exit labels: Can be fixed over doors and indicate a safe exit route in case of emergencies.
- Caution and notice signs:Â Specifies PPE to be worn in certain areas like high visibility vests and protective boots and suits.
- Obstruction signs:Â Designates areas where workers should stay clear of, like forklift lanes.
9. Prepare for Emergencies
Planning for emergencies is one of the best ways to mitigate nonfatal and fatal incidents. You can inspect your warehouse exit routes and layout and identify potential safety obstructions like machinery blocking entrances. Testing and inspecting signage, lighting and alarm systems is vital for ensuring suitable lighting and cautions to mitigate a crisis.
You can also train staff for emergencies with first-aid training and emergency drills. Employees must select and train workers in first aid to provide immediate assistance in emergencies.
You must also ensure the first-aid kit has basic requirements like gauze and latex gloves. Emergency drills can help you and workers move to safety in a calm and organized way. It can also let you identify ways to enhance safety plans and routes with frequent exercises and evaluations.
Emergency drills can include:
- Allocating responsibilities to specific staff members to lead workers to safe exits.
- Timing how long it takes to exit the building safely.
- Designating routes for workers to follow to a meeting point.
- Clearing aisles and pathways and removing obstructions.
10. Report and Keep Track of Injuries
While you ultimately want to keep injuries to a minimum, it’s also essential to know when they occur and under what circumstances. Encourage employees to report any incidents. Get the names of the people involved, the location in the warehouse, the time of the incident and the details of what occurred.
A record of any injuries or issues allows you to track warehouse conditions and make changes to improve everyone’s safety.
Common Warehouse Injuries
Understanding common warehouse injuries like trips, slips, falls and machine entanglement can help prevent them. You can identify the cause of common injuries and find ways to remove the source. Here are some common injuries:
Heavy Equipment Injuries
Heavy machinery causes many injuries in warehouses, like fractured limbs, being struck by a forklift or being pinned between two pits. Heavy equipment can also cause fatal incidents. Machines can fall or overturn on workers, leading to fatalities. Employees can fall off forklifts and get caught in machinery.
Many heavy equipment accidents can happen due to losing control over machinery, poor supervision and limited warehouse access. Faulty or defective equipment and obstructions in pathways can also cause machine accidents and extreme injuries.
Machine Entanglement
Machine entanglement involves employees’ clothes, jewelry, hair or body parts getting trapped in equipment. Machine entanglement can cause nonfatal and fatal injuries. Warehouses have the machinery and moving parts — without proper signage and instruction, workers can get too close and get caught in equipment parts.
Exposure to Chemicals
Chemical exposure can cause severe injuries like burns and skin corrosion. Workers can get respiratory illness and skin irritations from chemical fumes and spills. While many chemical spills and leaks can be accidents, they can have serious side effects. Chemical spills can cause fires leading to burn injuries and toxic fume inhalation.
Overextension Injuries
Employees carry, pickup and move heavy loads like boxes and crates, leading to joint strain. Overextended or hyperextended joints can cause severe knee, elbow, neck and shoulder injuries. Overextension injuries can lead to hospitalization and long-term pain. Many employees can suffer extension injuries and continue working, worsening the condition.
Slips, Trips, Falls
Slips, trips and falls are among the most common injury causes. Workers can trip over machinery like pit forks and forklifts. They can also fall from a machinery operating box or a platform when loading and stacking racks and shelves. Workers can slip on liquid, chemicals, oils and wet surfaces and injure various body parts, leading to hospitalization. Many trip, fall and slip accidents can happen because of obstruction in pathways, malfunctioning equipment and chemical or liquid spills.
Improve Your Warehouse Safety With Quality Supplies from T.P. Supply Company, Inc.
Implementing safety in warehouses is vital. While many safety measures and supplies can help, you need quality, convenient, versatile and cost-effective solutions to maximize safety and affordability.
We understand how critical warehouse safety is. That’s why we offer new, used and reconditioned materials to meet your budget. We also provide transportation and installation services. We can help you improve safety in your warehouse with aisle shields, rack guards, guardrails and machine guarding panels.
Browse our safety products, and contact us for quality safety supplies.