No products in the cart.
Machine Safeguarding
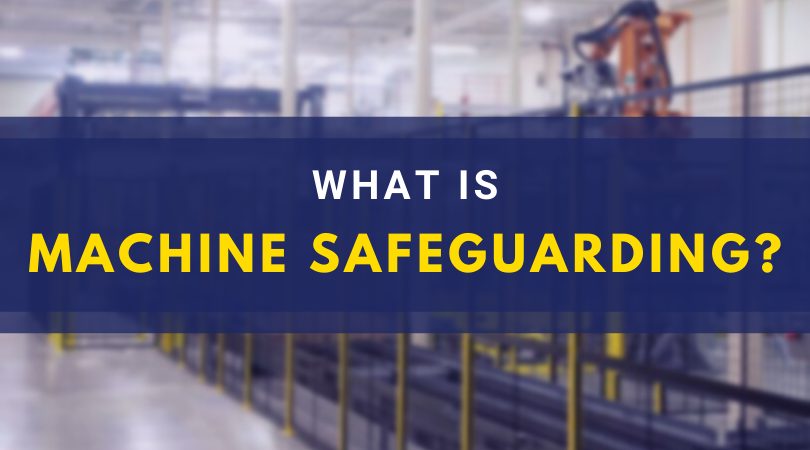
27
May
Machines are an integral component of many processes, but without the proper precautions, a machine’s moving parts can pose a risk to operators and maintenance crews in a wide range of industries. The Occupational Health and Safety Administration (OSHA) states that 18,000 injuries and 800 deaths occur yearly from moving machinery parts.
T.P. Supply Company, Inc. prioritizes proper protection in the workplace. We have machine-safeguarding products and solutions to keep employees safe at work. Learn more about machine safeguarding and how reasonable safety precautions can keep your workplace a safer, more productive environment for everyone.
What Is Machine Safeguarding?
Machine safeguarding is the process of preventing contact between moving mechanical parts and skin or clothing. It can also include controlling emitted particles such as woodchips or sparks. Machine safeguarding is a crucial component of safety across all industries. OSHA requires safeguarding to maintain a safe working environment as well.
Some typical applications include gates or panels covering the moving mechanisms or using guard enclosures to make sure the machine is not operating without the right conditions. There are plenty of size and mobility options depending on your needs.
Machine Safeguard Requirements
The first step to adhering to OSHA machine safeguard requirements is identifying potential workplace hazards. Once you identify the areas that need to be addressed, you can easily safeguard your machinery.
The basic hazardous motions are:
- Rotating
- Punching
- Shearing
- Bending
- Reciprocating
- Transversing actions
- Cutting
These actions all have a unique point at which they could contact the clothing or skin. For example, rotating cylinders may have burrs on the outside, which can snag and grip clothing. We’ll discuss the primary types of machine hazards in detail later.
The Hierarchy of Controls for Machine Safeguarding
The hierarchy of controls is an established method used to identify and rank safeguards to protect workers from hazards. They are arranged from the most to the least practical approach. While they exist individually, you may combine them for enhanced protection. Let’s look at each more closely:
1. Elimination
This control involves removing the hazard at the source by ensuring the risk no longer exists. For example, you can stop using the hazard-causing material or eliminate processes that expose workers to injury.
2. Substitution
Where eliminating the hazard or process is impractical, you can find a safer alternative. For example, you can switch to less hazardous materials or methods that rely on less speed, force, electric current or temperature. The key is to compare the new risk with the old and ensure the new introduction does not create equal or more severe risks.
3. Engineering Controls
These measures prevent hazards from coming into contact with the workers or reduce the likelihood of harm occurring. They include using protective barriers, equipment and workspace modification, ventilation creation, and more. For example, you can use guards to create barriers so workers do not interfere with the machine or block the hazard at the source before it comes into contact with a worker.
4. Administrative Controls
These established work practices reduce the frequency, duration or intensity of exposure to hazards. They change how the work is done or give workers more information about the risk through the following means:
- Procedures: Include equipment inspections, checklists, planned preventive maintenance, work schedule changes, employee rotation, pre- and post-task reviews, infection prevention and control practices, and lockout, tryout or tagout.
- Training: Involves educating workers on safe work procedures, hazard communication, permit-required confined space entry, and lockout, tagout or tryout.
- Warnings: Include using signs, backup alarms, computer messages, smoke detectors, labels, horns and instructions to call workers’ attention to dangers.
5. Personal Protective Equipment (PPE)
PPE refers to equipment worn to reduce exposure to hazards. Examples include safety glasses, gloves, hearing protection, respirators, protective clothing and hard hats. Providing this equipment is essential, but employers must also ensure employees wear it correctly. That’s why it’s so important to have an effective safety program.
What Guards Should Achieve
Safeguards must accomplish the following standards to comply with OSHA regulations:
- Prevent contact:Â The safeguard must provide a physical barrier that prevents clothing and other body parts from contacting the machine.
- Stay secure:Â Machine guards should be of high-quality materials and secured to the machine. Workers should not easily be able to bypass, tamper with or remove the machine guard.
- Stop falling objects:Â The safeguard should ensure that objects cannot fall into and disturb the moving parts.
- Allow safe maintenance:Â Workers should be able to lubricate and inspect the machine without going beyond the safeguard.
- Introduce no new hazards:Â Safeguards should not create any new hazards. They must not have jagged edges, burrs or rough materials, as this defeats their purpose.
- Create no interference:Â Any safeguard that prevents workers from performing tasks efficiently and quickly creates a challenge. Proper safeguarding can enhance efficiency by relieving the worker’s apprehensions about injury.
Properly using safeguards can save workers from injury without slowing down your operation.
5 Types of Machine Safeguarding
There are five main types of machine guarding you can use to protect workers. These are:
1. Guards
Guards are the physical barriers that prevent direct contact between the dangerous parts of the machine and people nearby. They work by enclosing the hazard-causing components, making them one of the most preferred solutions.
Guards are usually designed with bolts, screws and lock fasteners, and they require a tool for removal. The design is also made such that it does not obstruct workers from performing their functions. There are different types of guards you can use, such as:
- Fixed guards: Permanent guards with no moving parts. They are simple and mostly preferred to the others. The downside is that you may need to remove them for maintenance, typically requiring a trained professional.
- Adjustable guards: Permanent but manually adjustable guards you can lock to handle several material sizes. Employers must ensure that workers operating machines with these guards are thoroughly trained. Improperly locked or adjusted guards can fail and cause injuries.
- Interlocking guards: Designed to disengage or shut off when opened. They enable workers to access the interior parts of the machine without completely disassembling them.
- Self-adjustable guards: Similar to adjustable barriers, but they operate automatically depending on the stock size. Self-adjustable guards are typically installed on table saws and woodworking tools.
2. Devices
Safety devices are installed on the machines to perform various activities. For example, they can alert the machine to stop when a worker places their hands in the hazard area or require workers to use both hands when operating the machine so they are out of harm’s way. Safety devices can also create barriers that synchronize with the machine’s operating cycle or retain or withdraw the worker’s hand during dangerous operations.
Safety devices use different sensors or controls to mitigate risk exposure, including the following:
- Radiofrequency: Uses capacitance fields designed to stop the machine from operating when interrupted.
- Photoelectric: Uses light sources and controls to stop the machine from operating when interrupted.
- Electromechanical: Has a bar or probe that descends when a machine cycle is initiated. The machine stops when an obstruction prevents the probe or bar from descending.
- Restraint or holdback: Uses cables or straps connected to the operator’s hands to restrict movement within safe areas.
- Pullback: Uses cables connected to the operator’s hands or wrist, which pulls away when the machine starts.
- Two-hand control: Requires the operator to use both hands on the control buttons simultaneously. The machine will only work when operated in the right way.
- Two-hand trip: Requires operators to use both hands on two trigger buttons simultaneously to start the machine. They are typically used on machines with full-revolution clutches.
- Safety trip control: Uses pressure-sensitive bars to stop the machine when pressure is applied. These are designed to prevent injuries when operators lose balance or trip accidentally.
- Gate: Creates a movable barrier to protect workers before the machine starts.
3. Automated Feeding and Ejection Methods
The approach involves using robots to perform tasks, thereby eliminating human involvement. The robot can do things like loading and unloading stock, transferring objects, assembling parts and more. These tasks are usually mundane or repetitive.
4. Machine Location and Distance
There are two vital things you must do. First, examine the machine’s location on the site. Second, identify the hazardous parts of the machine. Doing these things helps you ensure the working area is safe and that the operator is aware and away from danger. This control method is an effective way to prevent accidents.
5. Miscellaneous Aids
These resources provide added safety by protecting workers within the immediate vicinity. Examples include protective shields, awareness barriers and hand-feeding tools.
Types of Machine Hazards
The three primary types of machine hazards are:
- Hazard motions: Include reciprocating motions, rotating machine parts and transverse motions. Reciprocating motions include sliding parts or up-and-down motions. Transverse motions are materials moving in a continuous line.
- Points of operation: Include areas where machines cut, bore, shape or bend stock.
- Pinch points and shear points: Include areas where clothing or a part of the body could be caught between a stationary object or moving part.
There are also nonmechanical hazards that can injure operators and workers within the vicinity. These include flying splinters, debris or chips, and sparks and splashes. Sprays created during a machine’s operation also fall within this category. You can protect your workers from injury by providing machine guarding and PPE.
Popular T.P. Supply Company, Inc. Machine Guarding Products
There are many ways to safeguard your machine. The most popular is exterior caging, which lets you see the device without accidentally touching the moving parts. Some available machine guarding equipment from T.P. Supply Company, Inc. includes:
- Machine guarding panels:Â These metal panels go around the outside of your machine to prevent accidental contact. We have multiple sizes to fit your machines.
- Machine guarding posts:Â Posts fit in with our panels and doors to connect each piece. You can place posts wherever needed to work around any unique machine aspects.
- Machine guarding door:Â When creating a protective system around your machines, you should ensure you can still access machine components. A machine guarding door is a simple addition that allows you to access the machine for tasks like starting, shutoff and maintenance.
Hazard Training for Employees
Besides introducing proper machine safeguarding tools, employers must train their workers to use the safeguard equipment and protect themselves. OSHA requires that employers provide safety training for their employees so that they can prevent injuries. This includes updated training to coincide with new equipment and any changes in OSHA regulations.
OSHA has external resources for training and other information related to machine safeguarding. Training your employees will help you get the most out of your safeguarding equipment and ensure all employees understand the risks. You can prevent workplace injury from moving machinery with the proper knowledge and tools.
Protect Your Machines With T.P. Supply Company, Inc
T.P. Supply Company, Inc. is a leading provider of material handling and industrial equipment. We are a self-contained business, so you can trust us to deliver expert services and high-quality products. We deliver products using our trucks and provide on-site installation with our own crew.
We offer new, used and reconditioned equipment for your business. Our economic choices work with different budgets and allow you to get the materials you need for your business.
Shop online and browse our machine-safeguarding equipment today. If you want to learn more about our products and services, contact us at your convenience to speak with a representative.